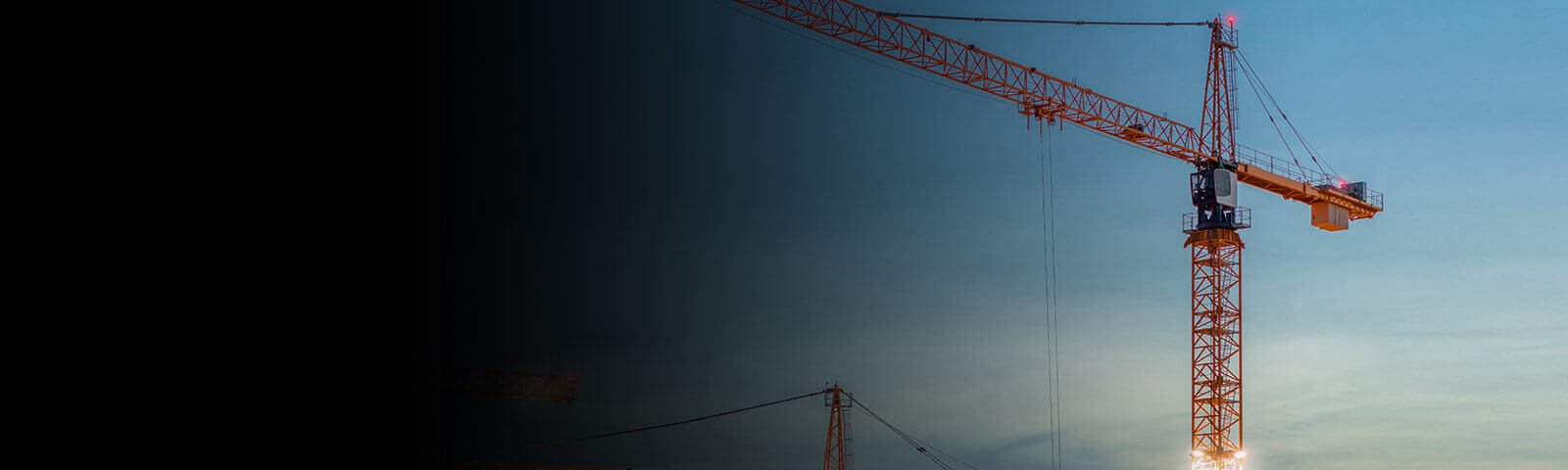
Contractor Customer:
Ensuring Crane Safety After a Move
Field evaluation and testing of crane assembly was required by the AHJ for a tower crane on a jobsite. Crane installation, unlike typical industrial manufacturing equipment installation, presents a unique challenge given their non-permanent location and often times their relocation after being evaluated for the first time in the field. In addition to the challenges in field evaluation of new or used equipment at facilities, tower cranes require particular attention when assessing their cables, especially when it comes to their sunlight resistance rating, and the specific type of overcurrent protection that exists for the motors, cables, and variable frequency drives. While certain types of motors on the crane are considered "short-time" (the hoist motor, for example) and don't require overload protection, other motors, such as the ventilation motors, do.
Business Issues
The crane required a new field inspection to review the electrical systems when it moved to another location to begin work.
- Needs approved by local AHJ before beginning operation
- Need a field evaluation, or third-party inspection, before AHJ will grant equipment approval
Solutions Provided
The tower crane field evaluation was requested by the customer within a specific time frame. Our field evaluation included the following:
- A field inspection of the equipment.
- Exposed non-current carrying parts of the equipment were verified to be effectively grounded in accordance with the applicable provisions of NEC®, Article 250.
- Wiring was verified to be properly sized, rated with a temperature rating suitable for the installed application, and properly routed throughout the tower crane.
- All internal electrical components were inspected for installation in a suitable enclosure.
- All major power components were evaluated to the appropriate Nationally Recognized Electrical Standard(s).
- Overcurrent protection was evaluated for compliance with the applicable electrical codes and standards.
- The equipment safety interlocks, emergency stops, operator controls and human machine interfaces (HMI) were verified to be properly identified and operating accordingly.
- etiCS team took field measurements to ensure equipment was working within manufacturer’s electrical nameplate ratings.
Project Results
All discrepancies noted in our preliminary report, as summarized below, were corrected by the client prior to our return visit to perform a final field evaluation in preparation for the inspection and approval by the AHJ, resulting in saving the customer time and money.
- The incorrect short-circuit current rating was listed on the nameplate.
- The control panel nameplate was not installed in a plainly visible location outside of the control panel enclosure, as required.
- The main primary overcurrent protection fuses were discovered to be oversized.
- The main disconnecting means for the equipment unmarked.
- Arc Flash and Electrical Shock Hazard warning labels were missing.
- Fuse replacement markings were missing.
- Overcurrent fuses for motor protection were oversized.
The client was satisfied with etiCS' field evaluation, and passed city inspection accordingly. They plan to continue using the eti Conformity team for its field evaluation needs in the future.
Related Services